Společnost se rozhodovala, zda jako srdce svojí chystané expanze na evropské trhy zvolí Česko, Slovensko, Polsko, Maďarsko, či Rumunsko. Rozhodla strategická poloha lokality s výbornou dostupností pro zákazníky napříč kontinentem od Německa přes Itálii a Francii až po Velkou Británii, zázemí kvalifikovaných pracovníků na českém pracovním trhu a podpora ze strany státu i Ústeckého kraje. Firma Nexen Tire zatím ukončila první fázi výstavby, v té následující mají přibýt další provozy. Jihokorejský výrobce do areálu o rozloze 650 tisíc čtverečních metrů ležícího těsně vedle dálnice D7 postupně investuje celkem 22 miliard korun. Po nošovickém závodu automobilky Hyundai Motors a kolínské továrně TPCA jde o třetí nejvyšší zahraniční investici do stavby nových provozů v Česku.
Nově otevřený závod na Lounsku vyniká vysokou mírou automatizace a robotizace všech procesů včetně logistiky. Jeho součástí je rovněž automatizovaný sklad, který je v současnosti schopen naskladnit a vyskladnit až 15 600 pneumatik denně.
Míchání gumárenské směsi
Než si ale pro nové pneumatiky přijedou k automatizovanému skladu kamiony najatých dopravců, projdou kaučuk, procesní oleje, karbon, silika a další chemikálie proměnou, jejíž úplné detaily žádná společnost nesděluje. V Nexen Tire se přesto rozhodli 831 metrů dlouhou výrobní halou provést novináře.
Jihokorejská společnost Nexen Tire patří mezi nejvýznamnější světové výrobce pneumatik. Její centrály se nalézají v jihokorejském Jangsanu a v Soulu. Patří mezi nejrychleji rostoucí výrobce pneumatik na světě. Má přes 500 obchodních zastoupení ve 137 zemích na celém světě a čtyři výrobní závody – dva v Koreji (Jangsan a Changnyeong), jeden v Číně (Čching-tao) a nejnovější, čtvrtý závod v Česku. Nexen Tire je průkopníkem v oblasti využívání nejmodernějších technologií a inovativních výrobních postupů.
Přírodní guma putuje z Asie po moři ve vratných obalech uložených v kontejnerech do evropských přístavů, z nichž ji do výrobní haly na Lounsku převážejí kamiony. Na kovových paletách pak vysokozdvižné vozíky dopraví materiál do automatizovaného vstupního skladu. Cisternová nákladní auta dovážejí do továrny oleje, které jsou přečerpávány do speciálních nádrží, stejným způsobem se do vyčleněných sil dostávají také karbon a plnivo silika.
Na samém počátku výroby je míchání uvedených gumárenských směsí a dalších chemikálií. "V horním patře je řada ručních násypek, kam se pomocí vysokozdvižných vozíků navezou jednotlivé chemikálie, které pak do nich operátor vhazuje," říká mluvčí Nexen Tire Europe Ivan Dzido. Zde hrají nezastupitelnou roli dva čelní vysokozdvižné vozíky Toyota. Dále polotovary mezi jednotlivými fázemi výrobního procesu přemisťují i laserem vybavené samořídící LGV vozíky Hanwha, podvěsný jednokolejový systém EMS (Electrical Monorail System) a pásové i válečkové dopravníky. Lidské ruce se pneumatiky dotknou až při vizuální kontrole a konečném skládání pneumatik do připravených kamionových návěsů.
Jednotlivá výrobní oddělení mají k dispozici automatizované subsklady, bez nichž by byla plynulost procesu nemyslitelná. Jejich přesný počet však společnost podobně jako v případě LGV vozíků nesděluje.
Výrobní logistika
Připravené dávky gumárenských směsí v Nexenu nejdříve kontrolují ve špičkově vybavené laboratoři, kde z každé šarže odebírají na detailní analýzu tři vzorky. Ty pak ukládají do dalších prostor v automatickém skladu, kde jsou též uchovávány textilní a ocelové kordy. Odtud je pak EMS systém automaticky převáží k dalšímu zpracování.
Moderní pneumatika je opravdovým hi-tech produktem, který se v současnosti běžně skládá z více než deseti součástí. Jednotlivé výrobní operace na sebe plynule navazují. Ze základních surovin se vyrábějí polotovary, jako jsou například běhoun, bočnice, nárazníky a vnitřní gumy, ale i výztuhy, zmiňované kordy či patní lana.
Běhouny a bočnice se tvarují na vytlačovacích strojích a posléze řežou, textilní a ocelové kordy se rovněž "porcují" na požadovanou délku. Patní lana, jež vyztužují patku a pomáhají udržet pneumatiku na ráfku, musí být pogumována. Tři řezačky se prakticky nezastaví, každá z nich je připravuje komponenty z daného materiálu, ať už jde o ocel, textilii či gumárenskou směs.
Během následujícího procesu konfekce se jednotlivé díly na dalších 12 automatizovaných zařízeních, takzvaných tire building machines, spojují dohromady a vzniká základní tvar surových pneumatik, označovaných v Nexenu jako green tires. Na tyto linky polotovary převáží na paletách LGV vozíky. Nelze si nevšimnout, jak se po ploše závodu pohybují bezpečně k určeným terminálům, a že vždy zpomalí či zastaví, přiblíží-li se k jejich dráze člověk (což se popravdě stává zřejmě jen při řídkých návštěvách lidí, pro něž je zdejší provoz novinkou).
Surové pneumatiky na vulkanizaci putují podvěsnou jednokolejkou EMS. Ve speciálních formách dostávají přibližně po dobu 12 minut při teplotě 120 stupňů Celsia svoji konečnou podobu a charakteristické vlastnosti včetně třeba vzorku na běhounu. Pro představu, jaký je tady "šrumec", byť z velké části očím případných návštěvníků zakrytý pláštěm všudypřítomných automatizovaných linek: proces vulkanizace probíhá na čtyřech linkách, v každé z nich je ve dvou řadách seřazených 40 "pecí", dohromady tedy 160.
Pak již na pneumatiky, kterých tady vzniká několik desítek typů, čeká několikastupňová kontrola kvality, na niž putují na dopravníkových pásech. První stupeň je vizuální. "Na této úrovni máme čtyři operátory. A pokud některý z nich najde něco neobvyklého, tak ještě před případným vyřazením pneumatiku posoudí ještě kolegyně z inspekce a další kolega," popisuje manažer kontroly kvality Miroslav Janega.
Po svislých dopravnících putují pneumatiky, které prošly vizuální kontrolou, dále na tzv. uniformity & balance zařízení, kde jsou podle přísných mezinárodních standardů posouzeny jejich dynamické a mechanické vlastnosti včetně primárního vyvážení. Poslední fází je rentgenová kontrola.
Sledování jednotlivých výrobních komponentů ve stručně nastíněném výrobním procesu umožňuje systém čárového kódu (e-paper), který je přímo integrovaný v patce pneumatiky. Díky tomu je každý kus registrován a monitorován ve všech Nexenem používaných logistických systémech: ASRS (Automatic Storage Retrieval System), WMS, MES a SAP. Každý jednotlivý pohyb po skladu je snadno dohledatelný i zpětně.
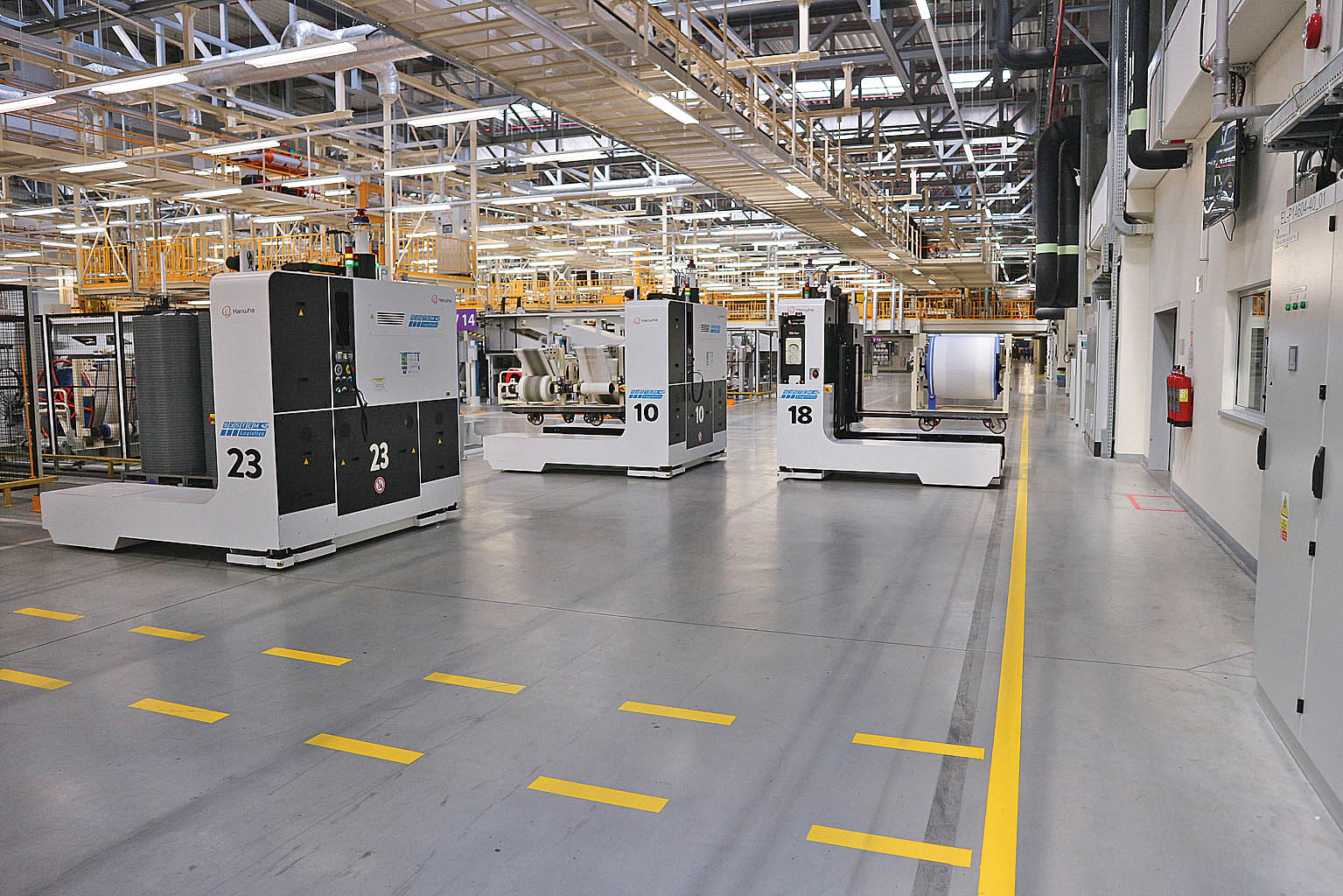
Automatizovaný sklad
Pneumatiky, které úspěšně prošly revizemi (je jich 99 procent), směřují do automatizovaného skladu. Díky informacím, které si každá pneumatika nese s sebou na zmiňovaném e-paperu, může být nasměrována a rozdělena dopravníkovým systémem ke stohovacímu jeřábu. Tento robot je vybaven senzory na její zachycení i odměřování výšky nad zemí. Díky tomu je schopen skládat postupně jednotlivé pneumatiky podle typu na podlahu do komínků po čtyřech či pěti tak, jak přicházejí z výroby, a následně je přesunovat v požadovaném počtu a umístění na palety (na jednu se vejde 16 nebo 20 pneumatik, podle velikosti konkrétního typu).
Manipulační jednotky jsou rovněž opatřeny čárovým kódem, který je propojuje s daným typem pneumatik a konkrétní skladovou pozicí. Automatické zakladače, kterých je tady devět, naloží příslušnou paletu přes válečkové dopravníky a s nastavením ve skladovém programu ji uloží na příslušné místo.
Do 50 metrů vysokého, 50 metrů širokého a 80 metrů dlouhého skladu s 18 regály se vejde až 360 tisíc pneumatik na 18 tisících paletových pozicích. Jeho provoz kontrolují během směny tři operátoři, kteří mají na monitorech svých počítačů detailní přehled o pozici a pohybu každé jednotlivé pneumatiky. Pokud by snad v některé fázi procesu čidla některý z kódů nenaskenovala, vždy může zaměstnanec zasáhnout ručně. "Princip je v zásadě podobný jako při skenování nákupů v supermarketu, přenos dat nemusí být vždy tisíciprocentní," říká manažer logistiky Vojtěch Fukal.
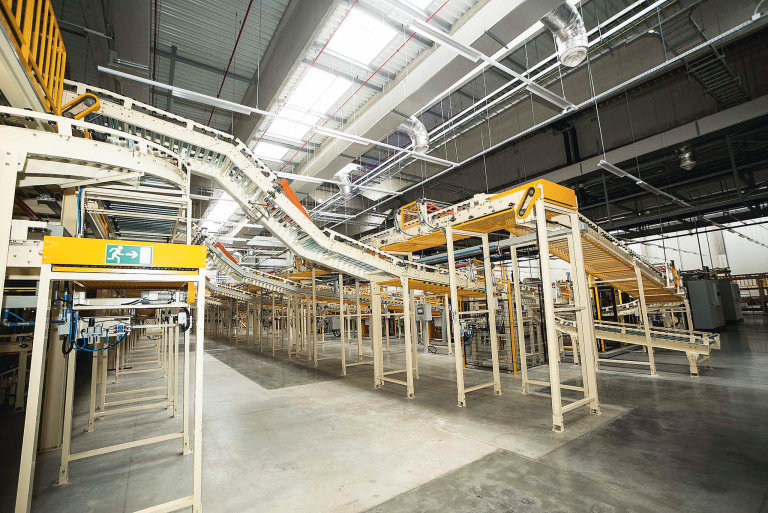
Při požadavku na odběr pneumatik jsou informace o jednotlivých kusech a jejich pozicích na paletách předány "vyskladňovacímu" robotu. Ten pneumatiky přemisťuje na dopravníkový pás, dávkovač je jednu za druhou směruje do takzvaného labereru, který pro ně automaticky tiskne a lepí štítky, s nimiž pak pokračují jedna za druhou šesti teleskopickými dopravníky až ke kamionům. V tomto okamžiku se pneumatik teprve podruhé dotknou lidské ruce − pracovníci Nexenu je v konečné fázi do návěsů, jež musí být vybaveny bočnicemi a zpevněnou plachtou, skládají volně zig-zag systémem.
Ruční systém nakládky je časově náročnější než manipulace s paletizovaným zbožím, ale do jednoho vozu se tak vejde až o 20 procent více nákladu. Jedno auto může odvézt 800 až 1200 kusů, záleží na jeho kapacitě.
Jak Vojtěch Fukal podotýká, někteří zákazníci si v rámci jednoho nákladu odvážejí 60 typů pneumatik.
Každou noc probíhá optimalizace skladových prostor. Roboti automaticky vyskladní všechny regály, přeskládají pneumatiky přímo na podlaze podle jednotlivých typů do komínků po čtyřech nebo pěti kusech, opět je umístí na palety a převezou zpátky na regály.
V silné konkurenci v letošním ročníku soutěže Impuls Logistika vydavatelství Economia a měsíčníku Logistika se automatizovaný sklad firmy Nexen Tire umístil v kategorii Top logistický projekt na čtvrtém místě. A to jsou v Nexenu teprve na počátku cesty.
Další rozšíření výrobních a logistických provozů záleží pouze na poptávce zákazníků. A zájem o pneumatiky jihokorejské společnosti, která vznikla už před 78 lety, mají renomovaní výrobci aut na evropském kontinentu čím dál větší.